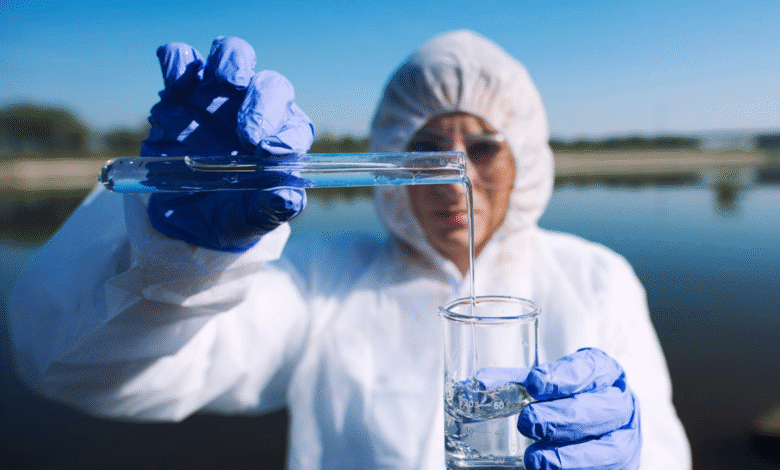
Polymer production is a complex industrial process that demands precision, efficiency, and consistent quality. As polymers form the backbone of countless products in industries ranging from automotive to healthcare, ensuring smooth and uninterrupted production is paramount. One critical but often overlooked component that significantly contributes to process reliability is the use of antifoulants. This article explores how antifoulant application enhances reliability in polymer production processes, improving operational efficiency and product quality.
Understanding Fouling in Polymer Production
Fouling refers to the undesirable accumulation of deposits on equipment surfaces during manufacturing. In polymer production, fouling commonly occurs on reactors, heat exchangers, pipelines, and filtration units. These deposits typically consist of polymer residues, catalyst by-products, and other contaminants formed under process conditions. Fouling causes a range of operational issues including reduced heat transfer efficiency, pressure drops, and potential contamination of the polymer product.
The impact of fouling extends beyond equipment performance—it can lead to frequent shutdowns for cleaning, increased maintenance costs, and production delays. In severe cases, fouling may even damage sensitive equipment, jeopardizing overall plant reliability.
Role of Antifoulant in Mitigating Fouling
An antifoulant is a specialized chemical agent designed to prevent or minimize the buildup of unwanted deposits on equipment surfaces. In polymer production, antifoulants work by modifying surface properties or interfering with the adherence mechanisms of fouling materials. This can include reducing the stickiness of polymer residues or altering the chemical environment to discourage deposit formation.
By integrating antifoulant solutions into polymer manufacturing processes, plants can maintain cleaner surfaces for longer periods. This directly translates to sustained heat transfer efficiency, stable pressure conditions, and reduced contamination risks. Consequently, antifoulants play a pivotal role in ensuring uninterrupted and reliable polymer production.
Enhancing Equipment Longevity and Operational Efficiency
The continuous application of antifoulants helps in preserving the integrity of critical production equipment. Heat exchangers and reactors, for example, benefit greatly from antifoulant use as they are particularly vulnerable to fouling due to their exposure to high temperatures and reactive chemicals. Cleaner surfaces mean less frequent cleaning cycles, which reduces downtime and extends equipment lifespan.
Furthermore, antifoulants contribute to energy savings by maintaining optimal thermal performance. Fouling acts as an insulating barrier, forcing systems to consume more energy to achieve desired process temperatures. With antifoulants, the process remains energy efficient, lowering operational costs and environmental impact.
Improving Polymer Product Quality
Reliability in polymer production is not just about operational continuity; it also hinges on consistent product quality. Fouling can introduce contaminants into the polymer batch or cause uneven polymerization due to localized temperature fluctuations. These factors compromise the physical properties and purity of the polymer.
The use of antifoulants mitigates these risks by maintaining clean and controlled reaction environments. This ensures that polymers produced meet stringent quality standards, enhancing the reputation and competitiveness of manufacturers in the market.
Integration and Best Practices for Antifoulant Use
Implementing antifoulant strategies in polymer production requires a tailored approach. Selection of the appropriate antifoulant depends on the type of polymer, process conditions, and fouling characteristics. It is essential to work with chemical specialists who can recommend formulations compatible with specific polymer systems.
Moreover, continuous monitoring and periodic evaluation of antifoulant effectiveness are crucial. Combining antifoulants with optimized operational parameters such as temperature control and flow rates maximizes their benefits. Training operators and maintenance personnel on antifoulant handling further ensures consistent application and safety.
Conclusion
In the demanding environment of polymer production, maintaining process reliability is essential for operational success and market competitiveness. The strategic use of antifoulant significantly enhances this reliability by preventing fouling, protecting equipment, improving energy efficiency, and ensuring consistent polymer quality. By investing in effective antifoulant solutions and best practices, polymer manufacturers can achieve smoother production runs, reduced downtime, and superior product performance.